Technical Information
Max Width= 4.5m
Max height= 3.5m
C2-high
Concrete boards
OSB
8-15 storeys (support core required)
Terracotta
HPL
Wooden slats
Exposed floor= 0.20 W/m²K
Roof= 0.14 W/m²K
Windows (w)= 0.8 W/m²K
EI60 - partition walls between dwellings
EI30 - partition walls
EI60 - ceilings
Schüco ASE 60mm lift & slide
Our Trusted Supply Chain

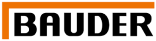
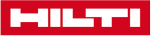
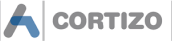
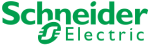
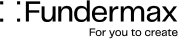
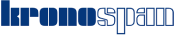

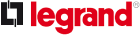
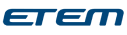

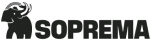


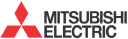

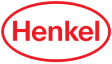
Accredited for Quality & Sustainability
We prioritize quality, safety, and sustainability in every module we create. Our certifications showcase our dedication to meeting and exceeding industry standards worldwide. From environmental stewardship to cutting-edge manufacturing excellence, these credentials reinforce our commitment to building a better future
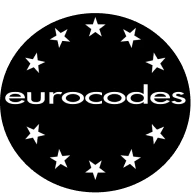
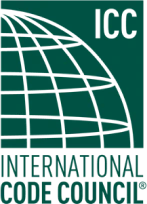
.webp)
The Benefits
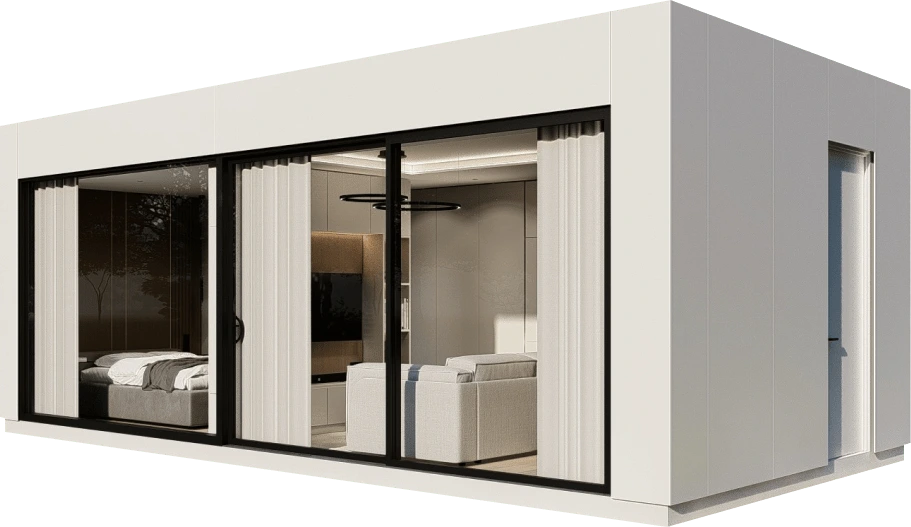
We apply car industry manufacturing precision to construction, assembling millimeter-accurate units in a controlled environment for top structural performance and quality.
Factory and on-site work run in parallel, cutting schedules by up to 50% and boosting productivity. Units, 90% complete, are ready for delivery in just 7 days.
Nearly complete units reduce vehicle movements by 80%, improving road safety. Simplified site work cuts wet trades, reduces workers by 60%, and minimizes noise, dust, and emissions
Built with hot-rolled steel and premium wood or concrete encasement, our buildings are durable and built to last generations.
Architects retain full design control, with the system accommodating complex shapes and diverse facade treatments. We can design projects from scratch or adapt traditional designs for our modular system up to the technical design stage.
Modular units move through the factory, while people, materials, and equipment remain stationary, boosting efficiency and minimising damage.
In some cases, we can add additional NIA (Net Internal Area) due to the efficiency of the volumetric walls.
Our process takes place in a clean, internal environment, carried out by long-term skilled operatives and using established supply chains. As a result, it is less susceptible to weather delays, cost fluctuations and skills shortages than traditional construction.
Our faster programmes ensure that developments open on, or ahead of, time, allowing clients to benefit from rental incomes and a quick return on initial finance. This in turn helps to reduce the interest costs on ongoing development finance and increases internal rate of return (IRR).
Not only do investors get an earlier return on their investment, they also get to phase the handover because of the minimal disruption on site. By the time we start installing volumetric units, it becomes an ‘installation site’ rather than a construction site.
Our factories offer workers a safe and clean environment. Crucially it reduces site personnel by up to 60% and transfers high-risk work at height to the safety of the factory floor.
The system has undergone both elemental and full-scale fire testing. External walls and facades are fully non-combustible. Our buildings have also been seismically tested to demonstrate they can withstand a magnitude 9 earthquake and are resistant to resonance vibration.
Our buildings meet the highest air quality, thermal and acoustic standards – all vital for health and wellbeing.
Our factory-based approach allows us to provide stable, long-term jobs and a less transient construction workforce.
By operating in a clean, safe, temperature-controlled environment, we can attract a wider pool of workers, which is vital to easing the construction skills crisis.
By employing regional talent, we ensure that our projects create job opportunities and stimulate economic growth in the areas we serve. Each modular unit we produce is a step toward strengthening the fabric of the community.
We Modular embraces the principles of the circular economy. We design out waste, maximise recycled content and use durable materials to give our buildings the longest possible design life.
Our streamlined process minimises carbon-intensive materials, waste and vehicle movements.
Our factory predominently relies on solar energy, via its roof panels.
Waste produced during manufacturing is recycled and on-site waste is reduced by over 80%. Therefore, less on-site waste means less skips and less waste in landfills.
The system is based on a lean, efficient structure, and the design process is front-loaded, with every aspect agreed before work in the factory begins. This means we can accurately quantify materials and order them to size from our established supply chains.
Common Questions, Clear Solutions
Our modules are absolutely NOT a container. Our Modular Construction system presents a comprehensive and superior alternative to conventional monolithic construction. By industrializing the construction process, we transcend the limitations of on-site building, human labor, and external factors. Instead, we fabricate in a cutting-edge manufacturing facility, overseeing every aspect on advanced production lines. Our method encompasses familiar construction stages — formwork, concrete pouring, plastering, painting— yet executed in a meticulously controlled environment, ensuring unparalleled quality compared to on-site methods.
Traditional construction is a lengthy and complex process, often taking 2-3 years and involving over seven separate stakeholders, each driven by their own priorities. This fragmentation inevitably creates stress for developers, with budgets and lead times frequently exceeding initial estimates. Worse still, the quality of the final product is inconsistent due to the inherent variability of on-site construction.
In contrast, modular construction offers a streamlined, predictable solution. With We Modular, the entire project—from start to finish—is managed by a single provider. Budgets are 100% pre-fixed, and project lead times are guaranteed. Off-site manufacturing minimizes construction-related risks while ensuring consistent quality, as controlled environments allow for precision and reliability.
Choose modular construction for efficiency, certainty, and exceptional quality.
Our Villa Collection is meticulously manufactured within 90 days of order confirmation, ensuring speed and precision.
For custom projects, timelines are tailored to the project’s size and scope, with lead times ranging from 150 days for single-family projects to 240 days for multi-family developments.
Delivery is streamlined, typically completed within 5-7 working days for Central and Western Europe. For other locations, delivery timelines are determined on a case-by-case basis to accommodate specific logistical requirements.
Our primary module type is constructed using high-strength S275 JR structural steel, with external encasing customized to client specifications, offering options such as OSB or concrete boards.
For orders exceeding 100 modules, we can provide reinforced concrete volumetric modules, delivering enhanced durability and scalability.
In the near future, we will introduce timber-framed volumetric modules specifically tailored for the markets in Germany, Austria, and Switzerland, further expanding our sustainable and region-specific solutions.
Our modular buildings meet all required standards and certifications, ensuring compliance with financial, regulatory, and insurance frameworks. This allows seamless integration into conventional funding, mortgage, and insurance processes, providing peace of mind and reliability for all stakeholders.
Build smarter. Live better.
Simplify your build with We Modular. Our system eliminates stress, reduces risks, and delivers faster, smarter, and more sustainable projects.